POWER FACTOR CORRECTION
- Home
- POWER FACTOR CORRECTION
POWER FACTOR CORRECTION
Power quality is critical to efficient operation of equipment. One contributing element to power quality is power factor. Power Factor Correction (PFC) aims to improve power factor and hence power quality, utilising capacitors to offset usually inductive loads, for example motors. PFC systems increase the efficiency of power supply, delivering immediate cost savings on electricity
When is Power Factor Correction right for you? Are you experiencing…
- Motor failure
- Electrical or electronic equipment failure
- Overheating of transformers, switchgear and cabling
- Nuisance tripping of circuit breakers or fuses
- Unstable equipment operation
- High energy usage and costs
How does Power Factor Correction work?
Power Factor is a measure of how effectively incoming power is used in your electrical system and is defined as the ratio of Real to Apparent (total) power where:
- Real Power is the power that actually powers the equipment and performs useful, productive work.
- Reactive Power is required by some equipment (eg. transformers, motors and relays) to produce a magnetic field for operation; however it does not perform any real work.
- Apparent Power is the vector sum of Real and Reactive Power and corresponds to the total power required to produce the equivalent amount of real power for the load.
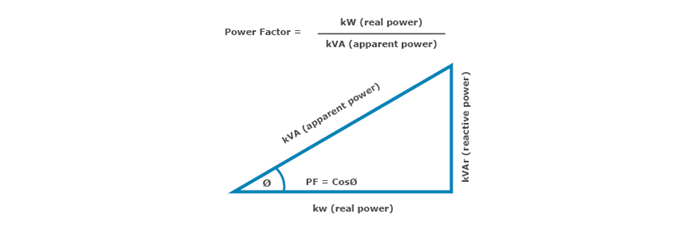
Power Factor Correction may be required where a system has a power factor of less than 90% (or 0.9). A poor power factor can contribute to equipment instability and failure, as well as significantly higher than necessary energy costs since it means that more current is required to perform the same amount of work. By optimising and improving the power factor, power quality is improved, reducing the load on the electricity distribution system.
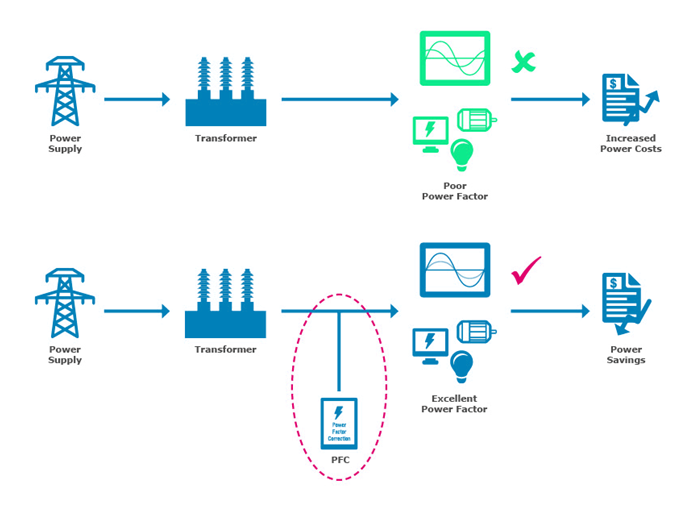
PFC equipment achieves a decrease in the total amount of electrical demand by using a bank of capacitors to offset an inductive load (or reactors if the load is capacitive).
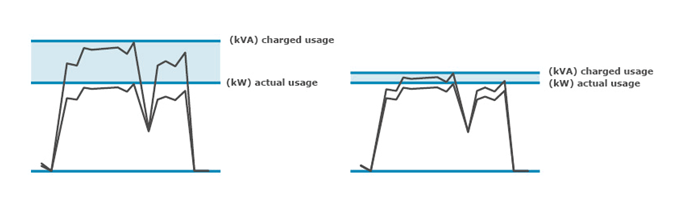
What we offer
Contactor switched Automatic Power Factor Correction panels
LV APFC Contactor Switched up to 3200 KVAR / 850 V
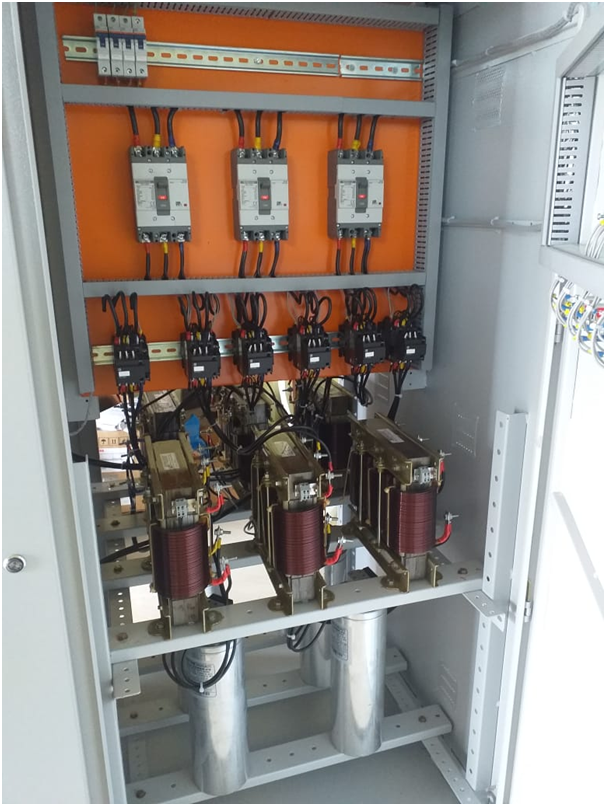
Outstanding features:
- Intelligent APFC with microprocessor based controller
- Automatic switching of PFC capacitors based on load variations of plant
- Designed to achieve power factor near to unity
- Available for balanced as well as un-balanced loads, 1-ph and 3-phase
- Less maintenance by optimized design, low loss and has long service life
- Display of all electrical parameters like KW, KVAr, KVA, p.f., THD, V, I , etc.
- Alarm output for low p.f., capacitor failure, overcompensation, over temp., under voltage, excess harmonics, etc.
- Auto/Manual Mode facility, protection for each capacitor feeders
- Light weight, compact design suitable for ambient temp upto 55 deg C
- Enclosures with CRCA sheet steel, seven tank pretreated, powder coated
- Data logging/operational facility through GSM, ethernet, RS485/232
- Manufactured as per relevant national and international standards.
- PFC capacitors MPP SH or Heavy Duty, Gas Filled or APP type capacitors
- Iron core harmonic filter reactors with Copper/Aluminum winding, low loss.
Thyristor switched Real time PFC – High speed electronic Switching
LV RTPFC Thyristor Switched upto 2400 KVAr / 690 V
Outstanding features:
- Latest thyristor zero-voltage switching system – cycle-to-cycle correction
- High speed – transient free switching of PFC capacitors within 40 to 60ms.
- Designed to achieve precisely unity p.f. near to unity to get max pf rebate and avoid leading p.f.
- Suitable for rolling mills, welding loads, DG set loads, ports, steel mills,cement and paper, etc
- Available for balanced as well as un-balanced loads, 1-ph an 3-phase
- Enhanced capacitor life due to transient-free, zero inrush current switching
- Maintenance-free because of static switching, no wear and tear of contactors
- Alarm output for low p.f., capacitor failure, overcompensation, over temp., under voltage, etc.
- Auto/Manual Mode facility, fuse/MCCB protection for each capacitor feeders
- Hybrid version also available – contactor + thyristor switching for cost effectiveness
- Enclosures with CRCA sheet steel, seven tank pretreated for anti-rust and powder coated, modular CNC construction also available
- Data logging /operational facility through GSM mobile, ethernet, Communication interferencesRS485/232
Our Power Factor Correction equipment maintenance includes checking that the system is operating at optimum performance levels. We check the following:
- Electricity load
- Voltage levels
- Harmonic content
- Detailed equipment condition
- Full functional operation
This level of maintenance is recommended by manufacturers to be undertaken every 6 months, or as required.
A comprehensive report is supplied on completion detailing the works carried out. It includes specific recommendations for consideration.
.